
Smart Materials in Haptic Technology as aids for the Visually Impaired
“Disability is caused by the way society is organized, rather than by a person’s impairment or difference. When barriers are removed, disabled people can be independent and equal in society, with choice and control over their own lives.”
— UNICEF (2017)
Project Background
There is approximately 285 million people worldwide living with a visual impairment and the rate of acquired blindness is expected to continue increasing.
Haptic technology is largely being incorporated into assistive devices since touch is their primary source of understanding non-audible information.
Problems with Current Haptic Technology
Large and bulky hardware
Loud
Sometimes produces unpleasant ‘mechanical’ feedback
Exploring solutions
Shape memory materials have the ability to make haptic devices:
Thin
Flexible
Light weight
The Project
The project focuses on exploring how currently available shape memory materials can be incorporated into haptic technology applications in order to improve the wellbeing and lifestyles of the blind and visually impaired.
Demonstration
How can smart materials effectively provide haptic feedback?
Perception
How are these new types of haptic feedback perceived?
Usefulness
Is it useful for the visually impaired?
The Research
Shape Memory Materials
Shape memory materials are smart materials that have the ability to recover their original shapes from a deformation when a stimulus is applied to them.


Shape Memory Polymers
PLA is a shape memory polymer which can be 3d printed. The shape printed is the form it returns to when a stimulus is applied to it after deformation. This material is activated with the help of hot water. It is capable of clear shape recovery but it may reduce over time.
Shape Memory Alloys
NiTi (Nickel-Titanium) and NiTiCu (Nickel-Titanium-Copper) alloys are the shape memory alloys which were tested. They come in the form of wires and can be treated in a ceramic oven at 400°C in order to program it to remember a specific shape. When activated with electricity, it showcases quick shape recovery. Shape memory alloys were selected to to move forward with since they are safe to use in close proximity to skin.
Exploring Actuators
Shape memory alloy wires were then incorporated into different formats of actuators in order to test their abilities of proving haptic feedback. Some of the formats can be found in the following videos.
The Demonstrator
After exploring different types of actuators, it was decided that the demonstrator should be able to provide multiple types of feedback.
The final demonstrator consists of three shape memory alloys in the form of springs. It is capable of two different types of feedback- dragging (in two directions) and squeezing.








The Build

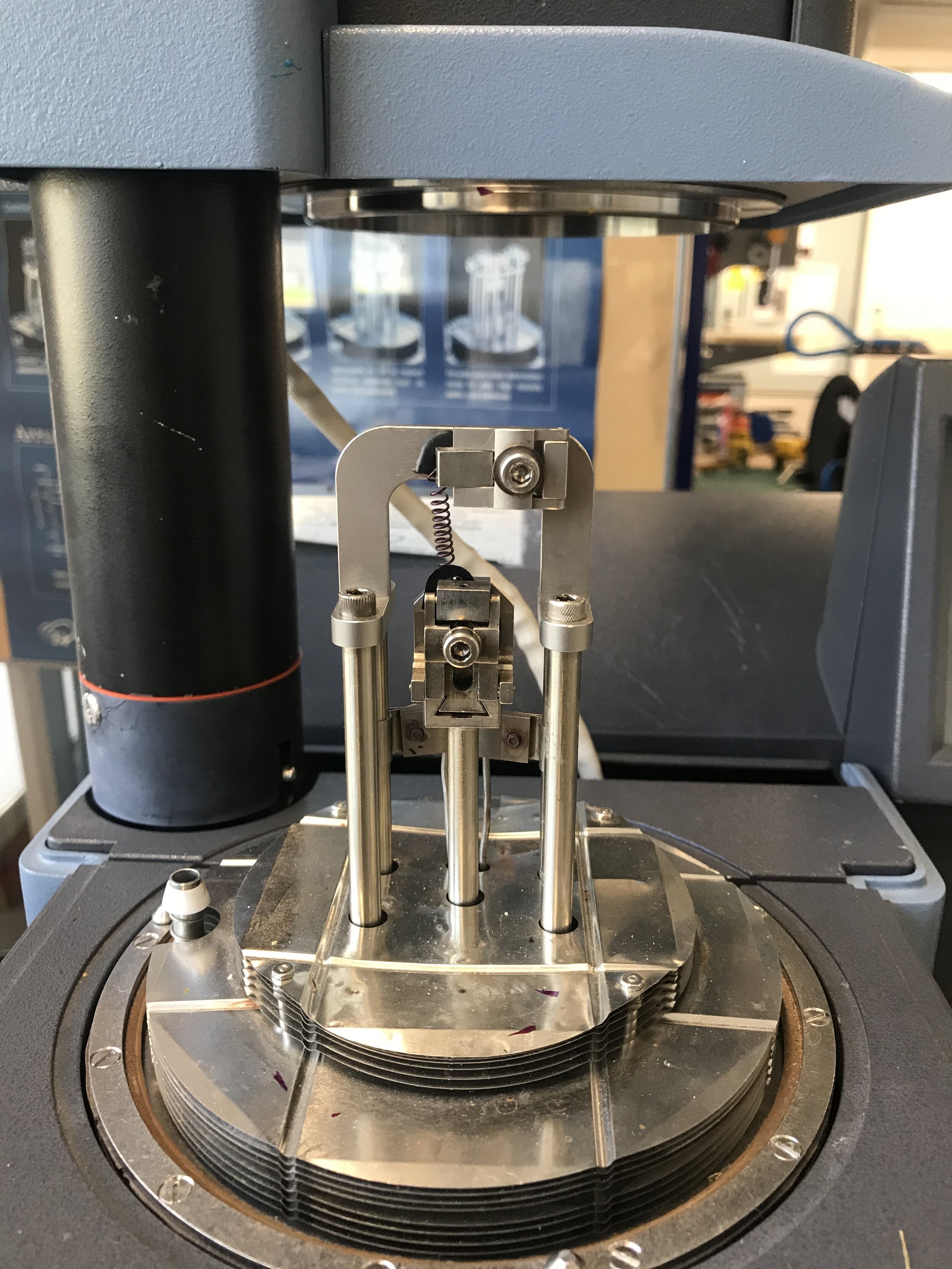

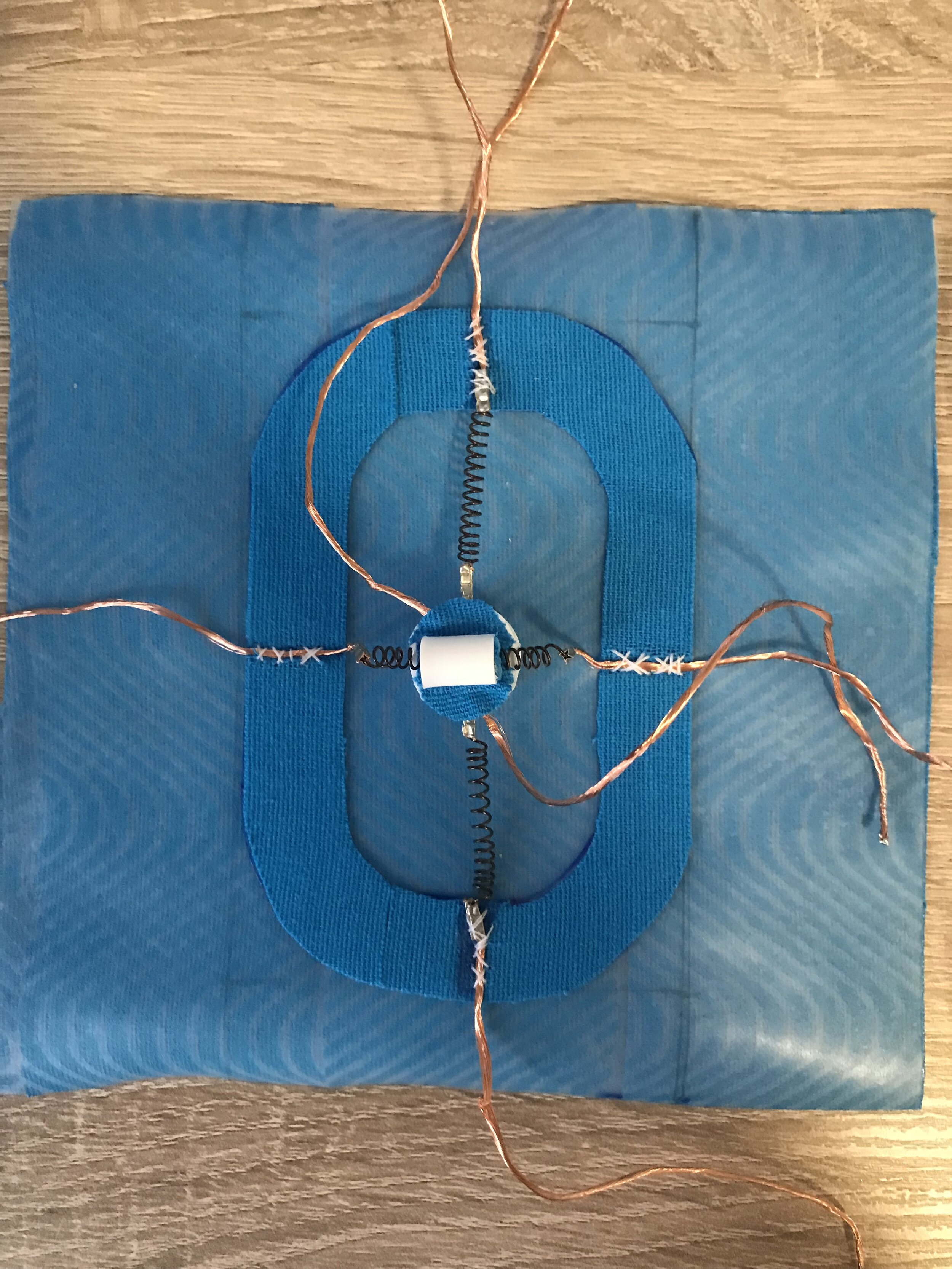

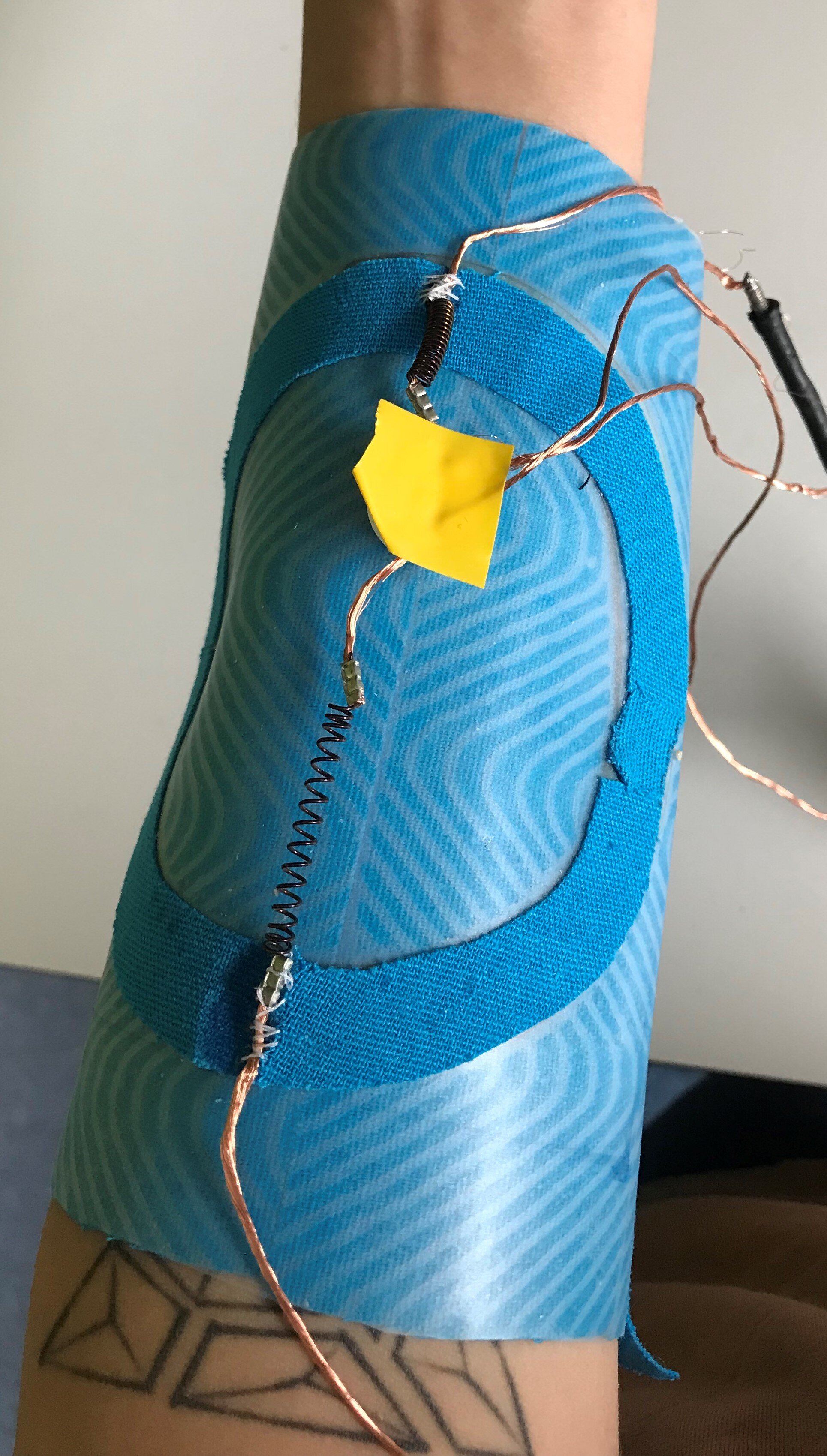
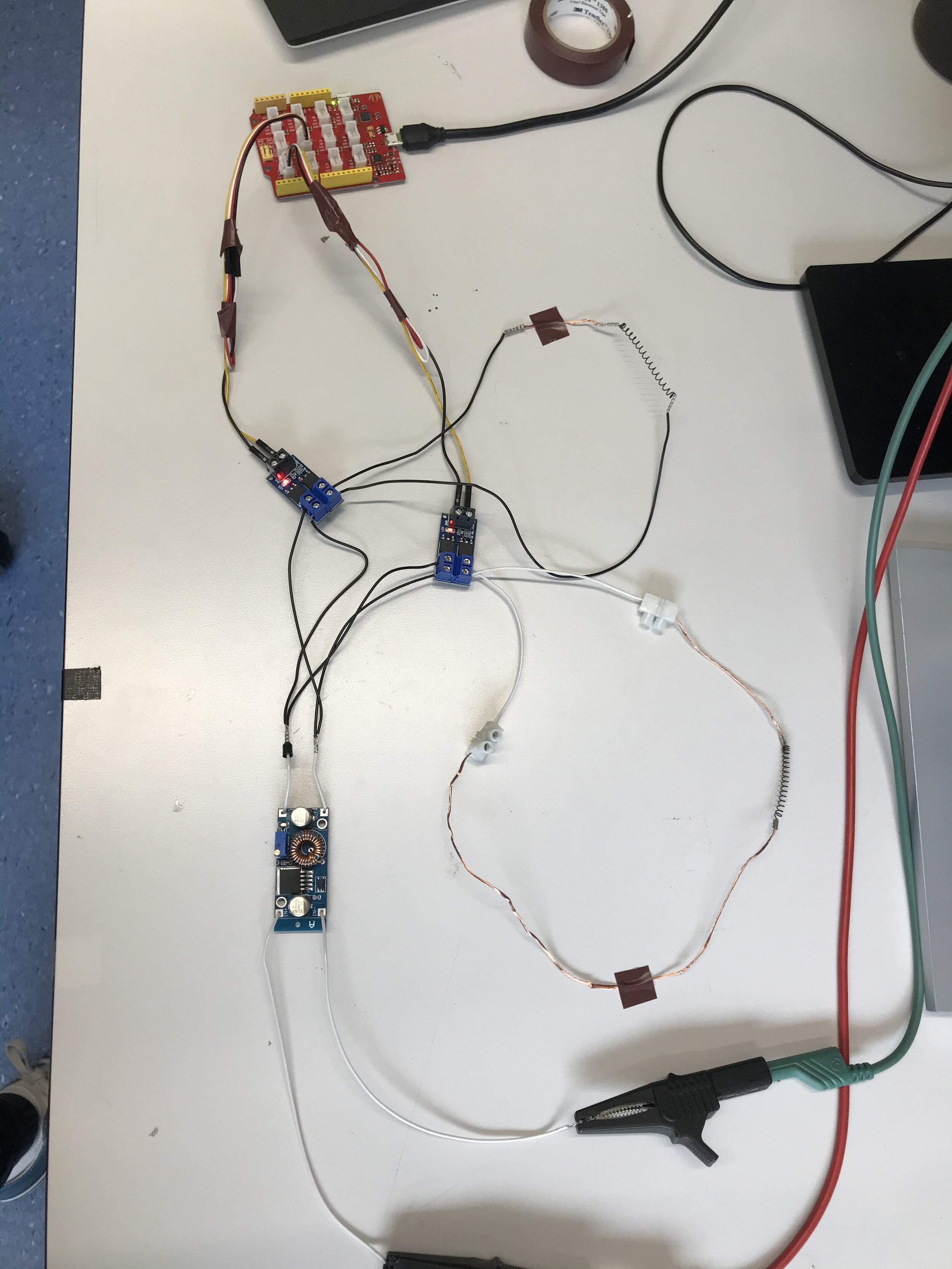
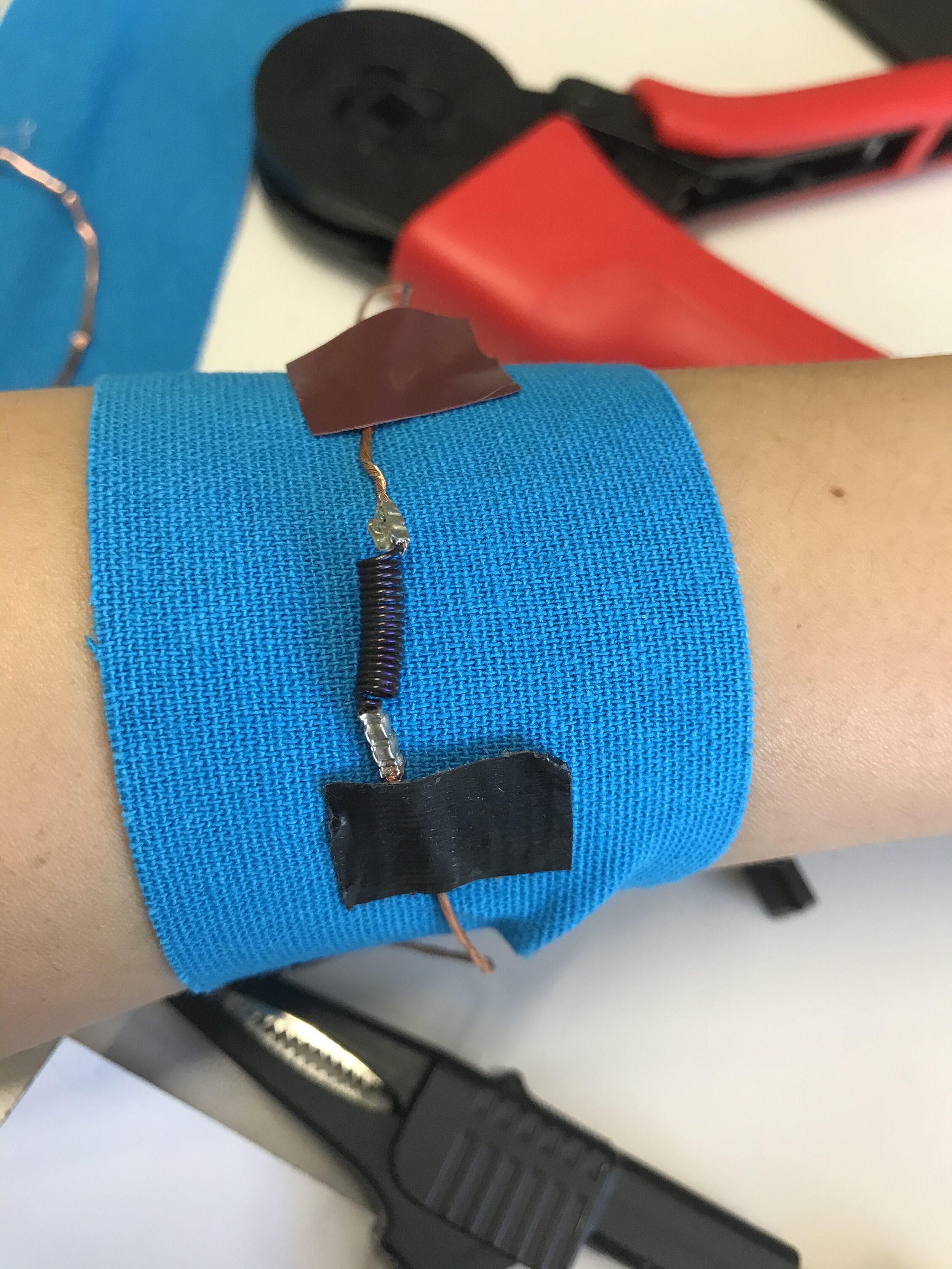
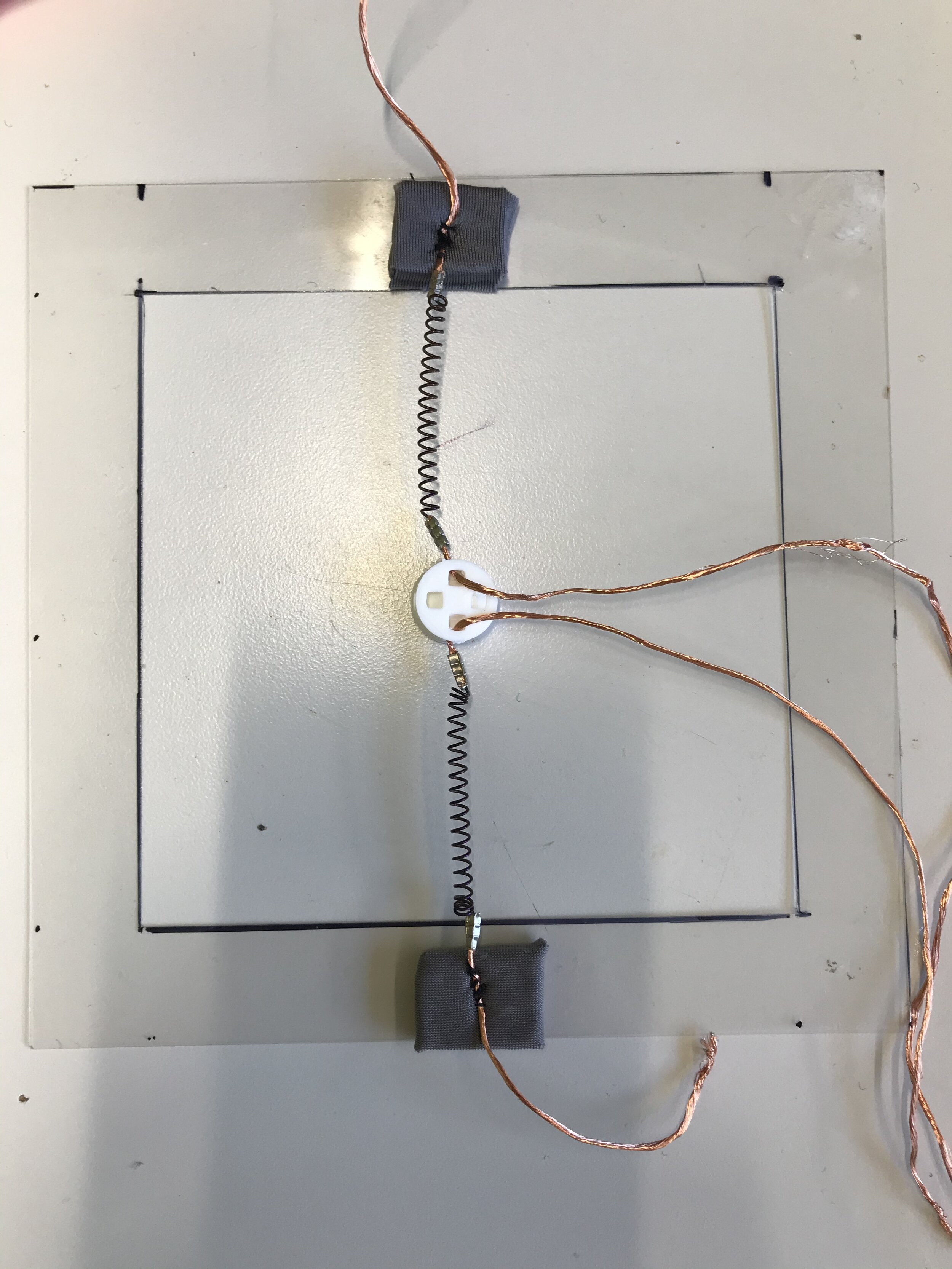
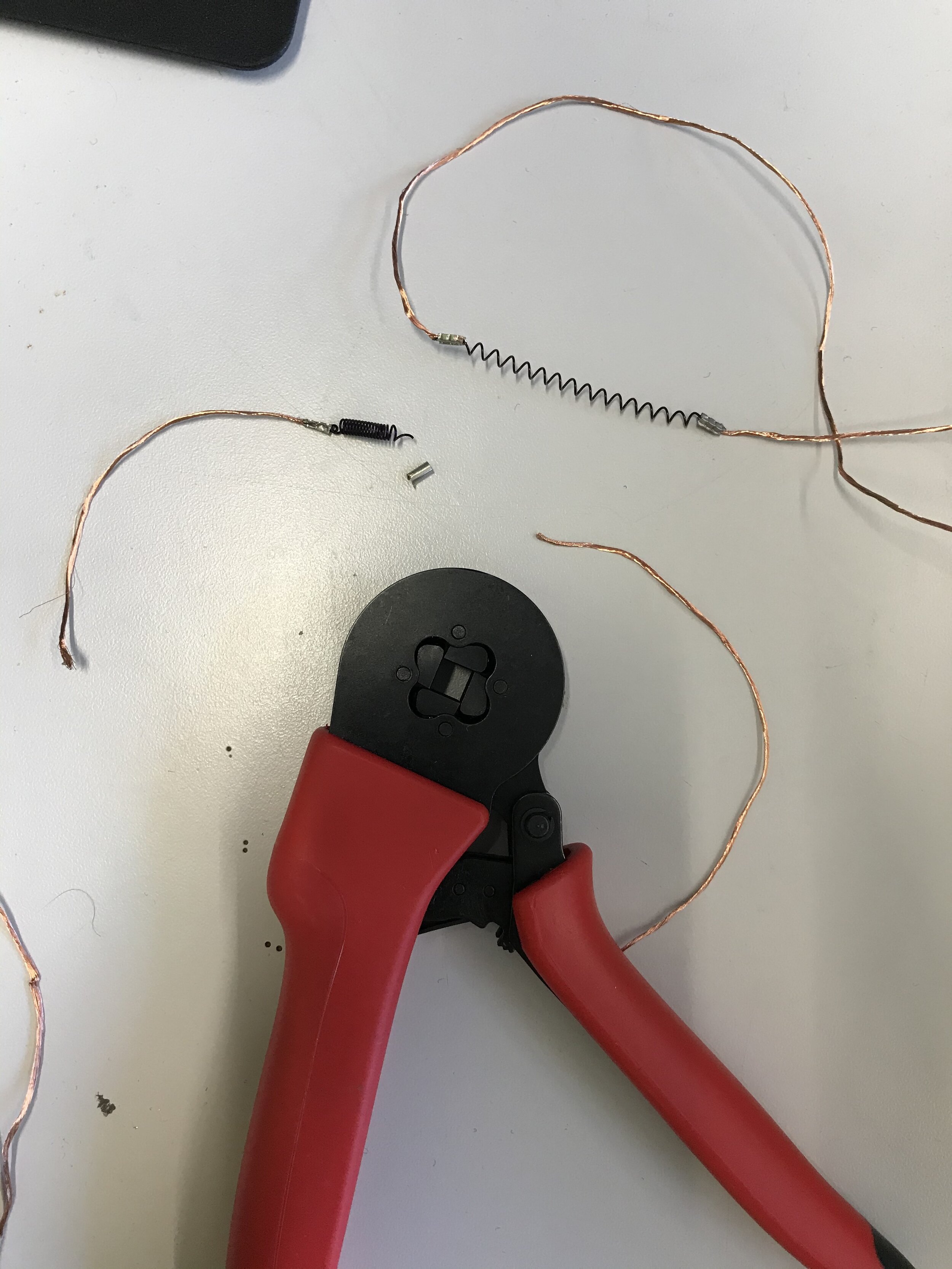

Testing with the Target Group
Testing was done with 4 participants having different types of visual impairment.
Purpose:
What sensations are perceived?
Are they distinguishable?
Could this type of feedback be useful?





Sensations:
“Organic and natural”
“Wheel moving along the arm”
“Finger on the skin”
“Massage”
“Non-directional pressure”
Distinguishable feedback
Recommendations
The technology is to be further worked upon to reduce the size of the electronics. It was recommended that the feedback and purpose of the future device be customizable to specific needs.
For example:
Navigation
Obstacle detection
Aids to crossing traffic
Remote care
Project Details
Graduation Thesis Project 202i (individual)
Duration: 6 months
TU Delft (Netherlands)